Industrial water: essential guide to pollution, treatment & solutions
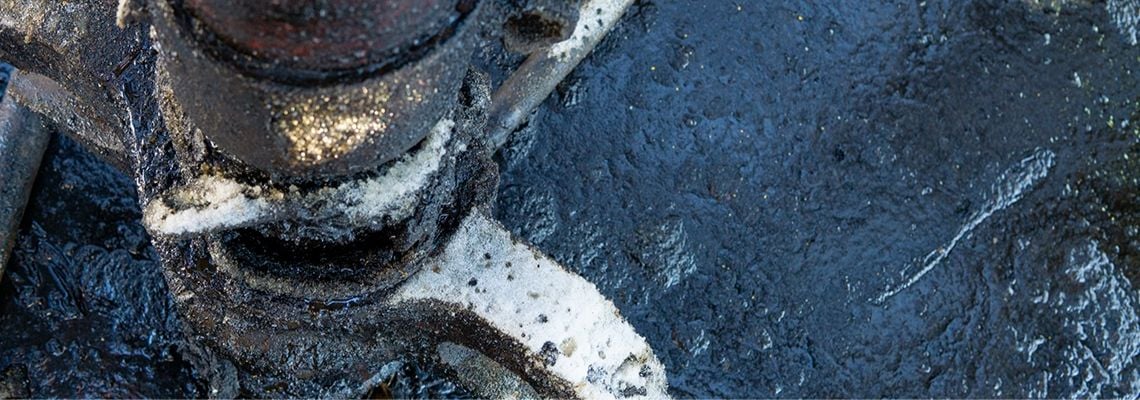
Table of Contents
- Industrial Water Usage
- What is Industrial Water?
- Water Positivity: a Barometer of Corporate Sustainability Efforts
- Four Industrial Uses of Water
- What is Industrial Water Pollution?
- Industrial Water Treatment
- Industrial Water Quality Requirements
- Industrial Water Solutions
Industrial Water Usage
Without water, many companies and the products they provide would fail to exist. Water use is a fundamental commodity for nearly every step of the manufacturing and production processes around the world.
Whether it's deionised water for electronics and pharmaceutical sectors, or softened water for boiler feed applications, water is necessary and comes embedded in the footprint of virtually every item created on the planet.
And to put it into perspective: industry accounts for around 40% of total water abstractions. Yet, at the same time, many global companies have manufacturing facilities operating in water scarce parts of the world, with over two thirds of companies now reporting exposure to water risks.
This article is designed to provide an essential guide to everything you need to know about industrial water and wastewater.
What is Industrial Water?
Manufacturing and other industries use water during the production process for either creating their products or cooling equipment used in creating their products. According to the United States Geological Survey (USGS), industrial water is used for fabricating, processing, washing, diluting, cooling, or transporting a product.
Industrial water and wastewater is a by-product of industrial or commercial activities. Whether it's the food we eat or the products we consume, water is required for nearly every step of production across a multitude of different industries. The resulting wastewater must be carefully managed.
Depending on the product being manufactured and the raw water quality in the region, different levels of treatment technologies will be needed.
For example, for medical, electronics manufacturing and food processing, deionized water is an essential ingredient. Called ultra pure water (EUP), this has almost all the minerals, dissolved gas and dirt particles removed from the water which could otherwise interfere with the manufacturing of precise and sensitive products, such as circuit boards.
Meanwhile, feed water is used in boilers and cooling towers to ensure efficiency, maximise boiler and system life, reduce maintenance costs and maintain levels of operational performance.
Industries that have a high usage of water and need for treatment include: brewery and carbonated beverage water; dairy industries; sugar mills and refineries; textile manufacturing; pulp and paper mills; oil and gas; the automotive and aircraft industries and many others
Water Positivity: a Barometer of Corporate Sustainability Efforts
Many multinationals aim to achieve “water positive” status by 2030, committing to return more water to communities than they consume in operations, as part of their broader water stewardship goals.
Amazon Web Services aims to achieve water positivity through efficiency, sustainable sourcing, community water reuse, and replenishment. Similarly, Microsoft’s 2030 strategy, part of its broader environmental plan, includes water positivity alongside carbon negativity and zero waste goals.
Elsewhere, computer chip giant Intel has already achieved its water positive goals in the US, Costa Rica and India, returning 13 billion out of 16 billion gallons used annually to “surrounding communities”.
As many industrial facilities use freshwater to carry away waste from the plant and into rivers, lakes and oceans, there is a responsibility to ensure pollutants are removed and minimised.
Given the heavy manufacturing taking place, industrial water can contain a multitude of pollutants, including: lead, mercury, nitrates, phosphates, sulphur, oils and petrochemicals.
Four Industrial Uses of Water
Heavy water using industries can include food, paper, chemicals, refined petroleum, or primary metals. Below is a list of how water is used within several industries.
1. Ultrapure water use in semiconductor manufacturing
Water is an essential component for the manufacturing of semiconductors and chips which are used everyday in computers, cell phones and automobiles. Ultrapure water is used throughout the process, including to remove impurities from silicon wafers. For example, a single 8” wafer, which is the foundation for approximately 100 chips, may require up to 2,000 gallons of UPW. As a result, semiconductor producers are focusing on ways to recycle, reuse and reduce the amount of water needed for operations. One notable case study is US firm Intel, which is creating its biggest water-reuse development as part of its new D1X factory in Hillsboro.
2. Cooling water
Cooling systems are used to remove heat from processes or equipment. Heat removed from one medium is transferred to another medium, or process fluid, which most often is water. According to the SUEZ Water Technologies Handbook, the driving force for the transfer of heat is the difference in temperature between the two media, which in most cooling systems, is in the range of 10-200 °F.
Many of the properties of water, including the behaviour of the contaminants it contains, are affected by temperature. As a result, the tendency of a system to corrode, scale, or support microbiological growth is also affected by water temperature.
3. Water use in the oil & gas markets
Globally the oil and gas industry represents less than 5% of total withdrawal but the sectors have an important role to play in protecting the quality of water in the areas they operate. Water is a raw material used and produced in high quantities in the oil industry, from extraction activities through to refineries and petrochemicals. Uses include: injection water, production water, process water, wastewater, rainwater, cooling water, tank cleaning water, and others.
4. Water use in pulp & paper mills
Despite digitalisation prompting a move away from printed products, the pulp and paper sector remains one of the largest users of industrial process water in the US and the second largest in Europe. Water is intricately associated with 85% of all the three stages of paper production namely, pulp making, pulp processing, and paper/paper board manufacturing, and their associated activities of cooking, bleaching, and washing. A high quantity of water consumed in the pulp and paper industry is used only for processing, thus, leading to the generation of large volumes of contaminated wastewater.
What is Industrial Water Pollution?
As well as consuming vast quantities of fresh water for manufacturing, industries also produce wastewater often laced with waste by-products used during the process. Depending on the country and region, there are differing levels of regulations governing what can and cannot be discharged to the local waterways. The following are some examples of worst case water pollution, although it should not be read as a blanket statement for that entire industry globally.
Textile manufacturing water pollution
Textile manufacturing has been called “one of the biggest polluters on the planet,” with textile mills said to generate one fifth of the world’s industrial water pollution. In China, for example, up to 20% of the country’s industrial water pollution comes from textile dyeing and treatment. It’s estimated that up to 20,000 chemicals are used globally for textile manufacturing.
Despite the high water usage of textile production plants, it is the wastewater being discharged – which can contain a cocktail of chemicals – that is equally a cause for concern. This wastewater can contain lead, phthalates, organochlorines and other chemicals that when disposed of into water bodies that will eventually reach water bodies for consumption, and can cause severe health problems and diseases in human beings.
Petrochemical water pollution
Petroleum refining has been one of the world’s largest industries. However, potential environmental hazards associated with refineries have caused increased concern for communities,
according to the EPA. The process of oil refining involves a series of steps that includes separation and blending of petroleum products.
Refineries are a potential major contributors to ground water and surface water contamination. Some refineries use deep-injection wells to dispose of wastewater generated inside the plants, and some of these wastes end up in aquifers and groundwater. These wastes are then regulated, depending on which country/region the site is operating in.
Wastewater in refineries may be highly contaminated, given the number of sources it can come into contact with during the refinery process (such as equipment leaks and spills and the desalting of crude oil). Taken together, land-based river and urban run-off sources constitute over half of the petroleum pollution introduced to North American coastal waters due to human activity, and 20 percent of the petroleum pollution introduced to ocean waters worldwide.
When wastewater from these sources enters the marine environment, it is usually by means of an estuary, an area where freshwater from land mixes with seawater.
Coal plant water pollution
Coal-fired power plants have been responsible for toxic metals, such as arsenic, boron and mercury, entering waterways, according to the Sierra Club. At one stage, 72% of toxic water pollution in the US came from coal-fired power plants. It was in 2015 when the EPA issues a rule to halt discharges in a move that was estimated to halt the release of 1.4 billion pounds of toxic metals, nutrients and other pollutants per year. However, under the Trump administration this regulation has been weakened, according to Scientific American.
Industrial Water Treatment
There are many uses of water for industry. Raw water entering an industrial plant often needs treatment to meet tight quality specifications. Meanwhile, used water also requires treatment to make it fit for reuse or disposal. In a nutshell, an industrial water treatment system treats water so it is more appropriate for a given use, whether it’s consumption, manufacturing, or even disposal.
Common industrial water treatment systems typically include:
- Raw water treatment systems
- Cooling tower treatment
- Boiler feed water systems
- Wastewater treatment systems
Raw water treatment systems optimize source water to enhance production efficiency and process performance for specific applications. These systems remove suspended/colloidal solids, iron, bacteria, and hardness. Examples include pre-treating water for cooling towers, boiler feeds, production processes, and drinking water. Raw water treatment aims to safeguard downstream equipment from scaling, fouling, corrosion, and other damage caused by contaminants.
Boiler feed water treatment systems shield boiler components from damage caused by contaminants like dissolved solids, suspended solids, and inorganic matter such as iron, copper, calcium, magnesium, aluminium, and dissolved gases. These systems work by removing harmful impurities and regulating the acidity and conductivity of the water before it enters the boiler.
Due to contaminants present in feed water, circulation water, and/or blowdown water, cooling tower water treatment systems are used to protect cooling tower components from damage. Such contaminants can include chlorides, hardness, iron, biological materials, silica, sulfates, TDS, and or TSS.
In industrial water management, a wastewater treatment system processes waste streams into reusable effluent or safely discharges it into the environment. Complexity varies based on compliance regulations and waste composition. Common steps include clarification, disinfection, softening, and distribution.
Industrial Water Quality Requirements
Industrial water quality standards vary based on application, region, and local regulations. For instance, ultrapure water for food and beverage manufacturing differs from that required for oil and gas extraction. Within these sectors, water quality also varies, such as for dairy, confectionary, soft beverages, and alcoholic beverages. Compliance is complex due to global and local regulations. Nonetheless, water used in the food industry must adhere to local drinking water standards or meet WHO Guidelines for Drinking-water Quality.
Even within the ultrapure water category, there are five grades distinguished by different standards. The term “high purity” water encompasses various specifications. Each grade serves multiple applications, such as:
- Deionised Water – medium pressure boiler feed, renal dialysis make-up, battery top-up;
- Purified Water – pharmaceuticals, cosmetics, chemical manufacturing;
- Apyrogenic Water – vial washing, tissue culture, water for injections;
- High Purity Water – high pressure boilers, combined heat and power systems, laboratories;
- Ultrapure water – micro electronics, supercritical boilers. Ultrapure water typically has a TOC limit of 0.05 mg/l as C and a resistivity of 18 Megohm/cm.
Industrial Water Solutions
Several industrial water solutions are available, influenced by factors like regional water quality, regulations, product requirements, and more. For instance, the methods for obtaining ultrapure water in semiconductor manufacturing differ significantly from those for treating wastewater in pulp and paper manufacturing. Municipal water treatment techniques, like membranes, are commonly adapted for industrial use.
Industrial water treatment solutions are often more diverse than municipal ones due to varied pollutants, concentrations, and temporal variability in industrial effluents. Below, we outline five industrial water solutions and processes.
Anaerobic digestion (AD)
Large amounts of organic waste matter are generated at industrial sites, including pulp and paper mills, which can be converted to renewable energy in the form of methane. Anaerobic digestion is the process by which organic matter is broken down in the absence of oxygen, in a sealed, oxygen-free tank called an anaerobic digester.
Anaerobic treatment of mill wastewater is widely accepted but is only applied to a few selected streams. Chemical oxygen demand (COD) removal rates in full-scale reactors range from between 30% to 90% with the highest COD removal rates achieved with condensate streams from chemical pulping (75-90%) and paper will effluents (60-80%).
Deionization (DI)
Deionization (DI) is the removal of all ionized minerals and salts from a solution through the process of ion exchange. Because most non-particulate water impurities are dissolved salts, deionization produces a high purity water that is generally similar to distilled water. Deionization filters operate by exchanging positive hydrogen and negative hydroxide molecules for the positive and negative contaminant molecules in the water. Positive chemicals like sodium, calcium, iron, and copper change places with the hydrogen molecules, and negative chemicals like iodine, chloride and sulfate change places with the hydroxide molecules.
This process is typically done by two ionized resin beds that are opposite in charges: cationic (negative) resin and anionic (positive) resin. Positively charged ions are removed from the solution by the cation resin in exchange for a chemically equivalent amount of hydrogen ions. Negatively charged ions are removed by the anion resin in exchange for a chemically equivalent amount of hydroxide ions. The hydrogen and hydroxide ions introduced in this process unite to form pure water molecules.
Membranes
Membrane technology has a significant part to play in the production of all grades of pure water. Depending on the feed water available, additional membrane technologies may be incorporated as pre-treatment technologies. Ultra filtration (UF) or microfiltration (MF) technology can be effectively used as a pre-treatment for reverse osmosis (RO) depending on the nature and variability of the feed supply to the water treatment system.