Tech Dive: Pumps - the unlikely hero of the energy crisis?
An essential part of any water operation for transporting volumes of water from one point to another, pumps are also incredibly power intensive, demanding high energy consumption to fulfil their roles.
While five years ago net-zero road maps were at the top of utilities and corporations' to-do lists, the ongoing geo-political situation that led to a signification increase in energy prices has seen innovations in pumps providing a quick-win solution to cut down the energy bill.
Could pumps become the unlikely hero of the energy crisis? In our latest Tech Dive, Aquatech Online takes a look.
Water's big energy question mark
Providing water and wastewater treatment services is extremely energy intensive. According to the International Energy Agency (IEA), the sector consumed 978 TWh (terawatt hour) of energy in 2020.By 2030, the IEA predicts this could rise to 1,252 TWh, and 1,473 TWh by 2040.
In the US, overall, drinking water and wastewater systems account for approximately two per cent of energy use in the United States, adding over 45 million tons of greenhouse gases annually, according to the US Environmental Protection agency.
An independent report from the IEA found that the water sector consumes four per cent of the world's total global energy, a figure that is expected to double in the next 25 years.
Of this four per cent according to Statista, 42 per cent of the energy is consumed by water-supply networks, 26 per cent by desalination and water re-use technology, 14 per cent by wastewater treatment plants, 13 per cent on water distribution and five per cent on water transfer.
And what do all these sectors all have in common? They all use pumps. Lots and lots of pumps.
How much energy does a pump use?
With four per cent of the world's energy being used by the water sector, how much are pumps responsible for?A tricky question to answer, with multiple variables that need to be taken into account.
For example, it requires less energy to pump surface water than it does to pump to groundwater. Similarly, the amount of energy it takes to pump water a long distance will be greater than it is over a short distance.
Other variables for pumping include the topography (affecting groundwater recharge), climate, seasonal temperature, and rainfall.
Where water is being pumped also plays a key role. In California, for example, 19 per cent of the state’s electricity consumption is for pumping, treating, collecting, and discharging water and wastewater.
At drinking water plants, the motors required to pump water can account for as much as 80 per cent of the plant's total energy consumption. Likewise, at wastewater treatment plants, pumps and solids processing take the top spots for energy consumption.
However, whereas one year ago utilities and corporations were happy to accept the fact that pumps are an energy-intensive necessity, Russia's invasion of Ukraine has only put a greater strain on the energy supplies and caused energy prices to soar.
Geopolitical strains
When Russia invaded Ukraine, energy prices shot up worldwide, reaching a 20 per cent increase for five months straight according to the Open Access Government.In the UK, the Guardian reported that Russia's invasion of Ukraine nearly a year ago had cost UK energy suppliers an additional £50 billion to £60 billion, on top of the £10 billion to £20 billion spent in a normal year.
Speaking to Aquatech Online, Matt Rolls, vice president of business development EMEA at Specific Energy, said: "What we’ve noted in the UK has been a drive in net-zero roadmaps, but pump have not always been at the top of their agenda. However, in the past six months as energy prices have soared companies are looking for quick wins in reducing these escalating costs."
As a result, a lot of companies are looking at ways to cut their energy costs and increase their savings, and innovations to reduce energy consumption in pumps could play a role.
But what are the latest innovations in pumps and who are the key players?
Specific Energy
Source: Specific Energy
Specific Energy doesn't build pumps, they've built the technology that allows pumps to run at their optimal speed for maximum energy efficiency.
Created back in 2010, Specific Energy was formed when someone called needing something that didn't exist.
Founder, Perry Steger, received a call from a water utility manager asking what the best speeds were to run their pumps and does it matter so long as the desired water flow is reached. In short, yes. It does matter.
Steger looked around for a product that could figure this out, but there wasn't one on the market and so Specific Energy was created to do just that.
"Our first deployment was back in 2011, now we have around 180 installations and over three million hours of proven runtime in the field," says Rolls.
Its solution is called the Dynamic Pump Optimizer, comprising a small box that can be retrofitted to any water or wastewater pumping system, that collects and processes all the data on the network in real time.
''Specific Energy is saving its customers an average of 14.7 per cent in energy savings.''
Essentially the hardware is a small industrial computer roughly the size of decks of playing cards that can monitors everything from sensors, valves, tanks and of course, pumps.
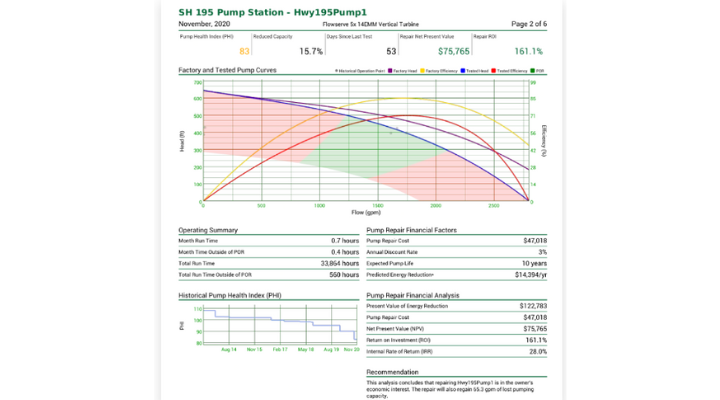
It solves millions of non-linear equations at the edge and feeds the information into a dashboard to allow the operators to see exactly how their pumps and system are operating and adjust ensure correct operation and achieve maximum energy efficiency.
"We build a physics-based model, a digital twin of the entire pump system, using existing plant data we build this digital twin model so we're able to compare modelled conditions against actual conditions and use that insight into what's happening on the upstream and downstream side of the pumps," said Rolls.
"These are the things that influence the efficiency of the pump systems, particularly as it relates to energy consumption. If you've got some change to suction side conditions or discharge side conditions, that could affect both power consumption and operational resiliency," he added.
Specific Energy said it is saving its customers an average of 14.7 per cent in energy savings, with some customers recording energy savings of up to 44 per cent. "The conveyance and transportation of water are one of the highest energy consumers. So being able to make gains in energy efficiency there can be quite impactful to their overall energy profile."
Danfoss
Source: Danfoss
Danish engineering company, Danfoss, has for a long time been in the energy efficiency game.
Georg Herborg Enevoldsen, head of innovation at the company, believes a change in attitudes to deploying smart pumps is where the next level of energy savings can be found.
He told Aquatech Online: "Pump wise we are looking to go to the next plateau.”
"We are chasing that, our best energy efficiency rate is 90-92 per cent but we believe we can go to 93, 94, maybe even 95 per cent."
Danfoss has developed a range of high-pressure pumps which is one of its fast-growing divisions seeing its technology grow in diverse markets from reverse osmosis to gas turbines, to cleaning and humification and firefighting.
"There is potential to improve the energy efficiency of these but it is all about not pushing them too hard.”
Its APP pumps, the 30, 38, 65 and 78 are the company's flagship energy-efficiency pumps.
The APP 78 has a max flow rate of 345 gpm and can operate at a maximum of 1,500 rpm.
"There is potential to improve the energy efficiency of these, but it is all about not pushing them too hard.
"Say you're driving your car and you are doing 120 mph, you're not going to get good mileage. If you drop it down to 40 mph you get better efficiency, it's the same with pumps, if you don't run the pumps too close to the upper limit, then you get these 90-92 per cent efficiency numbers out of them," Enevoldsen told Aquatech Online.
Enevoldsen believes this mentality is becoming more common in the sector.
"We're getting plant directors saying, "I don't care how much energy I spent, I care how much I have to pay for it.". Plants are changing how they operate to variable energy models.”
"On windy days, the price of energy will be low, so you produce more water. When the wind is not blowing, then you can hold back because you are ahead of your production schedule.
"From a plant's perspective, you can benefit hugely, because you can produce at a lower cost."
Xylem
Source: Xylem
Global water giant, Xylem, recently celebrated the production of five million of its Flygt pumps.
Flygt Concertor is a submersible wastewater pump with built-in intelligence, was launched in 2016 and has since then resolved clogging issues in sewage systems all over the world.
Its user-adjustable performance and self-monitoring anti-clogging countermeasures make it suitable for a wide variety of applications and for high volumes of solids in the wastewater.
The Flygt Concertor pump is one of Xylem’s flagship pumps and the one of the first wastewater pumping system with integrated digital intelligence.
It uses an algorithm to scan the system each pump cycle and find the most efficient duty point, ensuring that the pump uses the least amount of power possible.
In addition to energy savings of up to 70 per cent, there is less wear and tear on the pump, for lower lifecycle cost.
“The upgraded stations have also reduced their energy consumption by up to 40% kilowatts a year.”
Recently, Scottish water utility, Scottish Water, ran a trial using the Flygt Concertor.
Jessy Parmar, global product manager for Flygt Concertor at Xylem, speaking to Aquatech Online, said: “The utility in Scotland responsible for 30,000+ miles of pipe serving 5.4 million people wanted to minimise callouts, increase resilience, and reduce operational costs as part of its pledge to become carbon neutral by 2045.
“The Flygt Concertor helped them improve asset reliability, reducing 56 hours/month of cleaning and monitoring to just two monthly checks, and reducing site visits by 99.8 per cent. The upgraded stations have also reduced their energy consumption by up to 40% kilowatts a year.”
The integrated control functionality of the Flygt Concertor was recently updated with Xylem’s new control solution, Xylem Nexicon.
It comes pre-programmed with all logic unique to pumping stations, with sump cleaning, pipe cleaning and operational analysis built in – and can also be customised through Codesys to meet a customer’s exact needs.
Coupled with the ability to use conventional and Concertor pumps in the same station, the update to Xylem Nexicon allows greater pump station flexibility and is ready to meet future needs and challenges with always up-to-date cybersecurity protection.
Grundfos
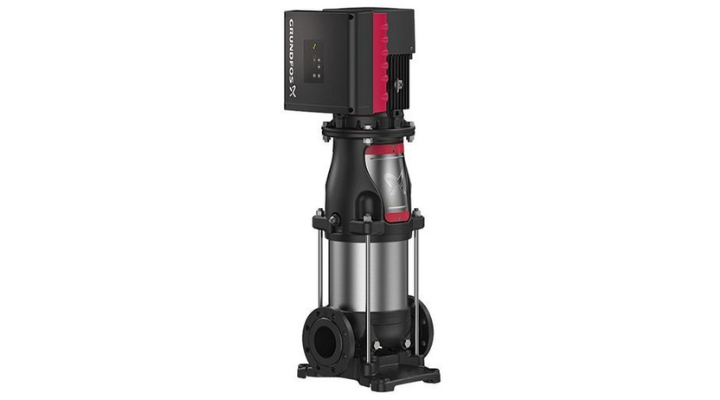
One of the world's largest pump manufacturers, Grundfos has developed its iSolution - a system of intelligent pump systems and water technology that looks beyond individual components and optimises the entire system.
iSolution is made up of intelligent pumps, cloud connectivity and digital services that enable real-time monitoring, remote control, fault prediction and system optimisation.
This year, Grundfos helped Britvic, a UK-based soft drink manufacturer, reduce its energy cost thanks to its pumps.
Britvic needed a solution that would deliver varying amounts of water, at the right pressure, and reduce energy costs and the carbon footprint for the site with remote access.
Grundfos installed its multistage CRE 95 pumps which operate on a 3-phase, fan-cooled, permanent-magnet, synchronous motor.
It features two dedicated digital inputs able to run a maximum of 3557rpm and a max flow of 146 m3/hr.
The installation of the pump along with a Grundfos dosing and disinfection system saved Britvic 45 per cent in energy costs.
Grundfos recently claimed that replacing what it estimates are 200 million old pumps with newer, more efficient models could save the world around 53.5TWh of energy each year.
Morten Bach Jensen, CEO of Domestic Building Services at Grundfos, said: “We must urgently address energy issues at the source, improving efficiency so we can manage demand and mitigate disruptions to supply.
“Replacing an old circulator pump with a newer, more efficient model is the number-one way that you can improve energy efficiency in a cost-effective way.”
What's next for pumps?
Pumps might be the unsung hero of the energy crisis but what is next for them?"There's going to be a constant evolution of the technology in itself," Rolls' believes. "Visibility for the user and providing the resilience and energy efficiency gains, that's always going to be a driver. But how that is going to be deployed I think will be slightly different.
"Utilities don't want to have multiple dashboards; one for their pumps, one for their treatment works, one for their distribution network, etc. they want to have a one-stop shop where everything lives.
"I think the beauty of digital technology is not just Specific Energy, but certainly something that we're working on at the moment is our ability to partner up with other technology providers and other platform providers, to deliver the real time analytics on the pumps and pump system as a component of an overall solution that addresses customer challenges," Rolls concluded.
Speaking on Danfoss' plans for the next five years, Herborg said: "In terms of our roadmap, for quite some years now, we have been focused on trying to maximise the value generated from our pumps.
"Making pumps deliver as much flow as possible, making them deliver higher pressures, making them out of more corrosion resistant materials, making them specific for offshore oil and gas, where they require special certificates on the materials.
"We have been squeezing the energy efficiency gap for the past ten years to 90-92 per cent and now we are looking for where the last few per cent are hiding. We believe in pump technology that has a wider range, where the energy efficiency stays high and how to exploit that.”
We promise never to send you spam and you can unsubscribe at any time!